They are very basic tools that help the management and quality specialists stabilize processes, enhance the quality level, identify nonconformities, vizualize the status and so on. The 7 tools of quality represent basic methods for lasting improvement in processes.
The reason why the tools of quality have come into existence
Preferably, every company needs to manufacture products and provide services the first time right. Each correction or fault that would make its way as far as the customer is exceedingly expensive. The reasons behind the existence of the tools of quality could be briefly summarized like this:
- to prove the quality that has actually been achieved
- to make the processing of data, facts and information more efficient
- to gain truly important factors of success
- to work only on meaningful problems
- to work in teams of experts
Nowadays, proving the quality is not good enough, you have to keep enhancing it. This is why there is the philosophy of continuous improvement, mainly by means of utilizing processes. For this particular purpose we have the 7 tools of quality which are here to help the management stabilize the processes and enhance the quality level.
The fundamental tools to improve quality in the company are the following:
Tool / Methods of Quality | Purpose / Mission of the Method |
---|---|
1. Collection of data and sorting out the information |
serves to acquire data about the work that has really been done |
2. Diagrams - Flow Charts | clarify the sequence of jobs/activities, and verify the appropriateness of places for collecting information and data |
3. Histograms | distribution of frequencies - it si a diagram that visualizes the facts gathered and their frequencies. It serves as a base to recognize dependencies. |
4. The Pareto Analysis | helps to identify the most important causes and their influences |
5. The Ishikawa diagram | it is a diagram that helps to identify the causes of problems |
6. The Correlation Analysis | it seeks to find potential relationships between the profile values |
7. The Regulation Diagram | it visualizes data in time and helps to uncover unwanted faults and non-conformities |
Using the 7 quality tools
The tools can be used both separately and all at once. It depends on the type of company and the problem that is being solved. Earlier they were used in the serial production. Then, gradually, the statistical process control, or the SPC, got into use more and more. A whole range of SW auxilliary tools have come into existence which are these days making data processing and data analysis a lot easier. In instances where there is no need to be using the statistical control, the 7 quality tools should suffice.
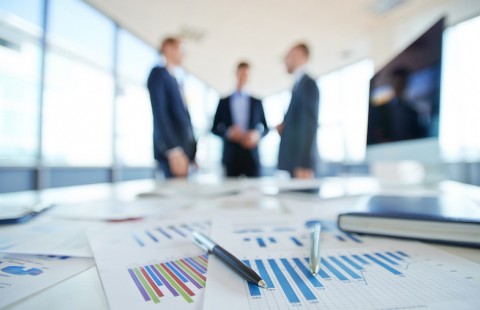
The Real | Interim Manager for Your Changes
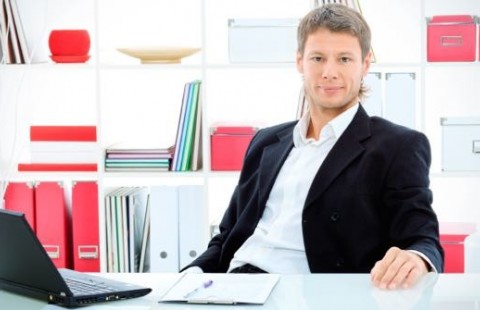
Manager work model
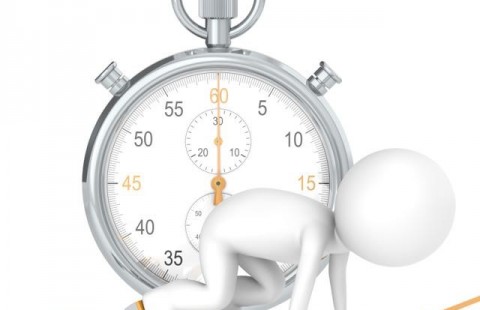
Time management - making use of time effectively
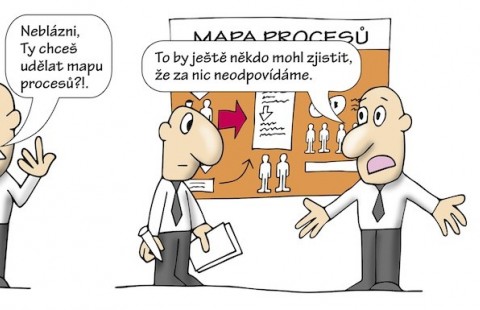
Jak správně tvořit mapu procesů
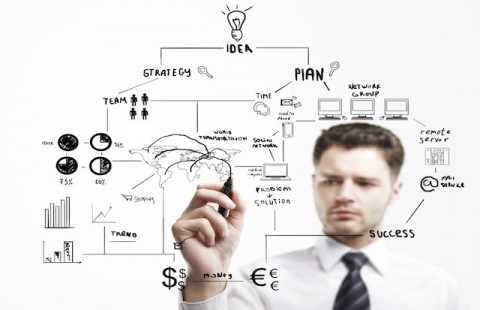
Modelling and setting the processes and procedures - ISO 9001
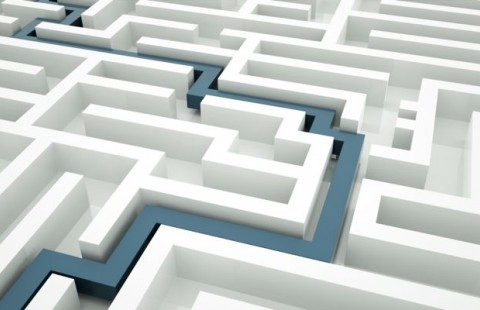
Training - preparation of the SWOT analysis and strategy
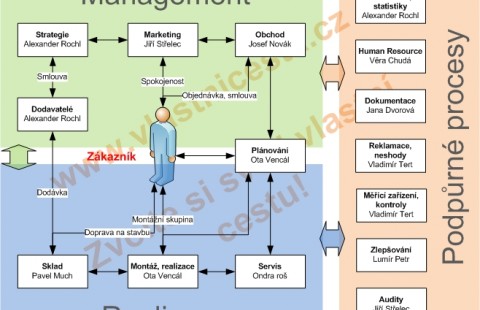
Company Management System of Quality Step by Step - ISO 9001
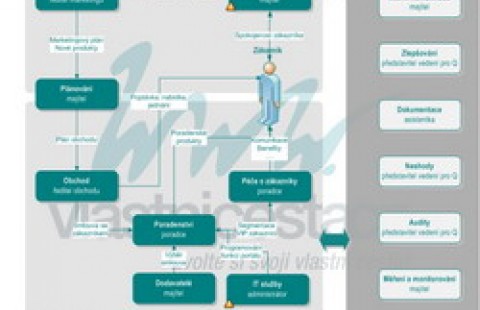
Process map acc ISO 9001 - business offer
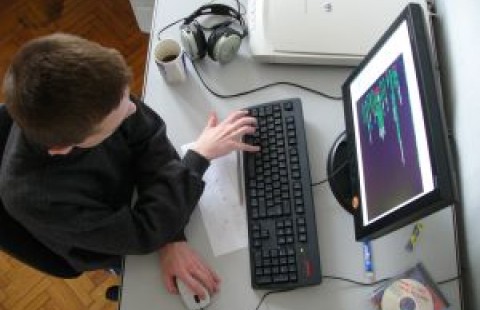
IT staff communication
Because of their simplicity and an ease of use, the 7 quality tools are nowadays also used in :
- services - confectioneries, hotels, ...
- preparation of SW - checking and evaluation of faults
- marketing
- Public relations
- and so on.
In many cases workers do not even know they are using one of the aforesaid quality tools.
The 7 tools of quality are focused on working with the so-called hard data. This is data that we have measured or are able to work with through numbers. Sadly, everything cannot be processed by means of hard data. Working with soft data sometimes takes preference. The article 7 new quality tools deals with working with soft data.
Have your consultant use a high quality approach based on attested methods!
Should you need a training/seminar on a given method, please, feel free to contact our consultants.