Here is a new case study by EDAG Engineering that demonstrates how competence and enthusiasm hand in hand can speed up the process of design and preparation of new product from the very beginning to the production of 10,000 a day. The creative people and designers from automotive can do it, in particular if they are not tied up by complicated and lengthy processes, which are rather common in this kind of industry.
At the beginning of April 2020 in Czech Republic, an unusual humming sound emanated from numerous households. People with sew machines has been producing ad hoc face masks in masse to comply to a new government issued order to wear a face protective gear in public as a countermeasure against a spread of novel Coronavirus and the COVID-19 decease.
At the same time a group of colleagues in the EDAG Engineering company Innovation Department decided not to stand by, but to use their skills and experience and try to invent a simple and practical solution to provide face masks that wouldn’t require elaborate sewing and could have be rapidly produced and distributed to as many people as possible.
Just two weeks from the idea to the production
Do you think it’s possible today to place an order for a new innovative concept and construction of a functional plastic part and to have first concepts and functional prototypes in your hand within just a couple of days? A final design in a week, the production of moulds ready just a little later and finally, fully running production AND distribution of thousands of units per day within just two weeks? Apparently, it is!
In this case, the team already scrambled got the idea during a weekend and in just a couple of days multiple designs proposals had been produced. From the beginning, their intent was to make use of 3D printing either in their company or by just anybody who possess the 3D printer themselves and would to be able to just download the designs for free.
Then, the project caught an attention of the colleagues in their parent company EDAG Engineering in Germany. There, the situation had been slightly different, no order had been issued yet, but it was anticipated in just a matter of days.
The original task suddenly changed significantly. There would be not only in house 3D print production and free to download files. Instead, the full production would be started in Germany using mass production plastic mould injection technology and would be immediately packaged and shipped thereafter. In addition, an extra multi-day supply of pre-cut fabric would be provided along the innovative plastic holder.
Enthusiasm and agility
Originally, a voluntary and enthusiastic endeavor changed its character to a serious contract. A suitable solution had to be invented to comply with both production technologies employed. Also, the fabric needed to be solved to have suitable properties. The Innovations Department team under a supervision of company director Aleš Paldus quickly switched to fully professional mode:
- Regular teleconferences with their colleagues at home office and in Germany
- Iterative and incremental development and agile development techniques
- Immediate print and testing of prototypes and materials
- And, most importantly, high personal commitment of all participants
The concept design quickly developed into a form of relatively small plastic clip into which a pre-cut piece of fabric could be easily inserted and fastened. Then as a whole, placed on the face without struggle and finally to be worn without discomfort.
Several fully functional prototypes had been produced employing various methods of fastening and wear while the technology, materials, packaging and distribution had to be solved as well.
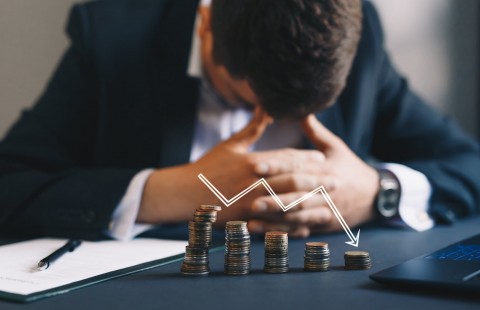
Legal aspects of insolvency and reorganization
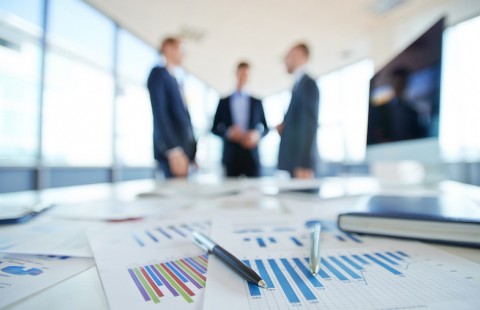
The Real | Interim Manager for Your Changes
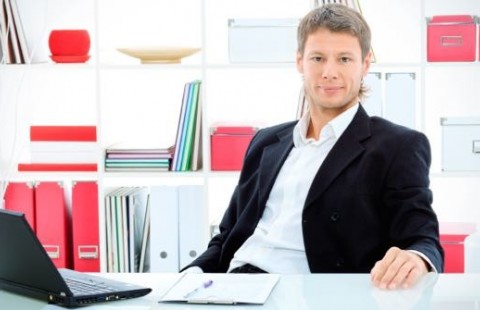
Manager work model
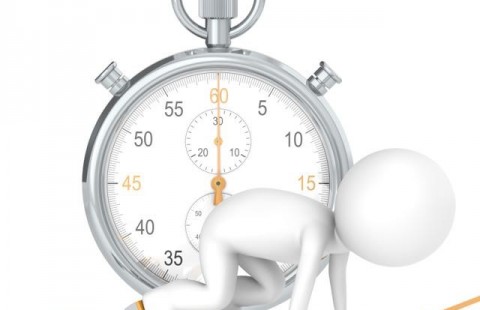
Time management - making use of time effectively
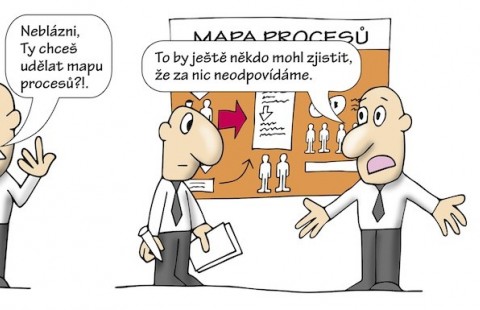
Jak správně tvořit mapu procesů
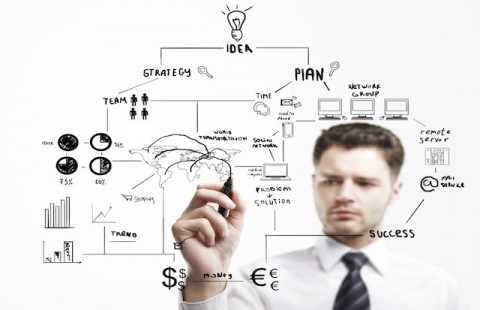
Modelling and setting the processes and procedures - ISO 9001
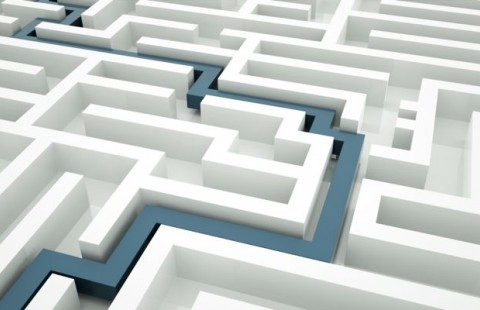
Training - preparation of the SWOT analysis and strategy
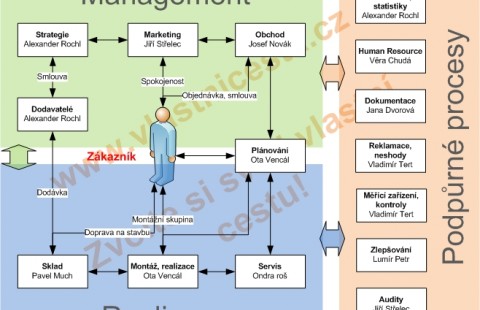
Company Management System of Quality Step by Step - ISO 9001
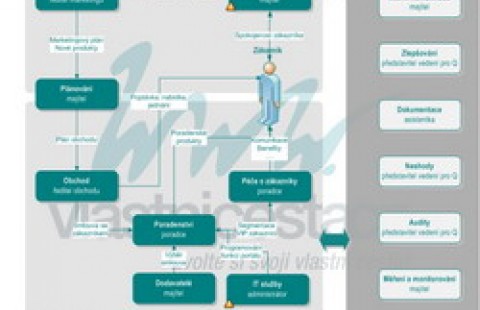
Process map acc ISO 9001 - business offer
In short:
in the second week since the first idea arose, first batch of
600 face masks was produced
and sent as a help to colleagues in the EDAG subsidiary in Spain, where the pandemic already become very serious and hard.
Meanwhile in Germany, new mould injection production was ready and running. First orders had just come – both local private business and government institutions immediately reacted to the offer and placed their orders. At the same time, the final and free of charge 3D print files were published on company website and 3D print sharing sites. Thousands of downloads and user modifications followed instantly.
At the beginning of May, the speed of daily production just surpassed 70,000 as two other companies joined the effort. By now, new EDAG MASK4ALL product is in stock in more than 30 regional supermarkets and several online shops in Germany. The masks have been employed in several government institution offices, regional hospital in Fulda city and in scores of small and middle companies as well. The cumulated order steadily increases and reaches one million.
Synergic transformation of Innovative Team
EDAG Engineering Czech company has been recently focused on automotive industry in particular. It provided wide range of services such as construction and production solutions, designs and calculations as well as innovations.
The management decided to change this approach, though. Foreseeing a possible diminution in automotive related orders, they decided to extend their portfolio by employing the innovations department in particular. Moreover, the approach and development techniques had the be changed. In automotive industry, a multiple years of development per one product is rather common. In other businesses though, it may be a matter of months, even weeks. Finally, the team has been expanded and creative people from other types of industry had been hired.
It seems this decision came just in time. The economy worldwide was hit hard by recent COVID-19 pandemic and the automotive industry in particular. The long time proven business strategies are suddenly failing. It seems that the most important task today is to offer a flexibility and creativity. To be able to seek quick and effective solutions and to deliver exceptional results much quicker that we might have been used to.
Support your creative teams or build the one just now to compete.