A Failure Modes and Effects Analysis is a structured method to identify and prioritize possible problems and their consequences in products, services, processes or projects that are being newly developed. Subsequently, it is used to assess measures taken to eliminate such problems.
History
The history of the FMEA method can be traced back to the 1940s, when the US Armed Forces were looking for a method to avoid failures in machines and equipment they were using. The method, then, successfully made its way - through space research and aviation - to the automotive industry where it has been applied most extensively and where it has become an integral part of a large family of tools to control quality. The method has been standardized through more than one document – MIL-P-1629, APQP,ČSN EN 60812, etc.
Principle
The principle of this method is based upon quantification of the frequency with which failures occur, how serious these failures are and how easily they can be detected.
1. First of all, potential failures need to be detected and:
- the consequences of these failures determined and assessed according to their severity,
- the causes of these failures determined and assessed according to their occurrence,
- inspection methods to prevent such failures determined, and the likelihood of these methods preventing the given failures assessed.
2. The RPN (Risk Priority Numbers) is then calculated by multiplying the above numbers. The calculation will give us the order of priority for corrective action.
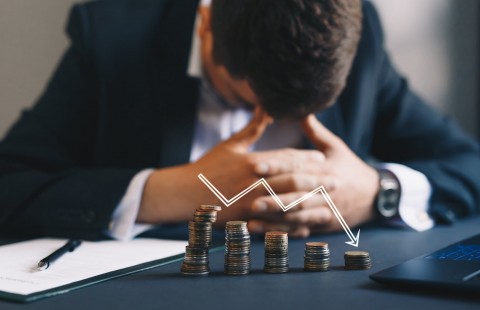
Legal aspects of insolvency and reorganization
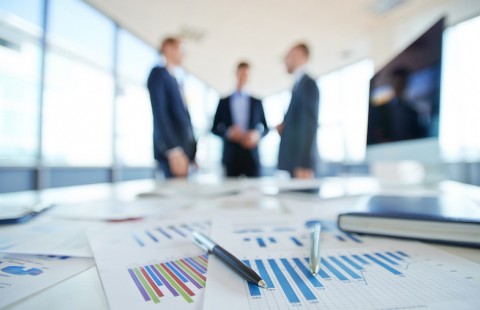
The Real | Interim Manager for Your Changes
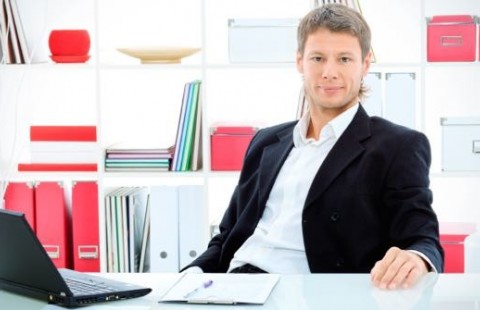
Manager work model
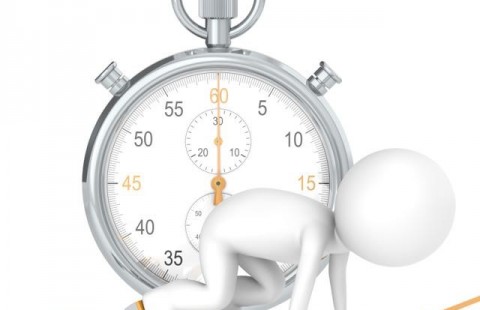
Time management - making use of time effectively
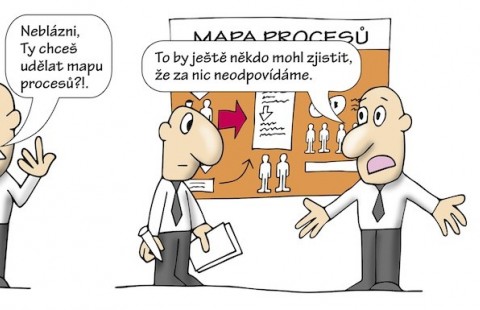
Jak správně tvořit mapu procesů
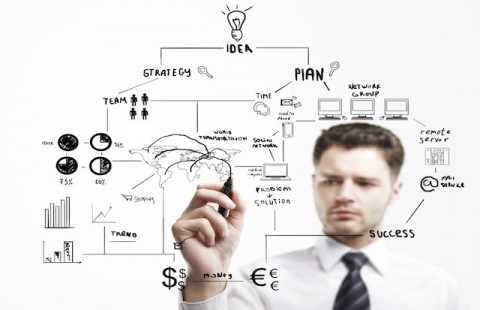
Modelling and setting the processes and procedures - ISO 9001
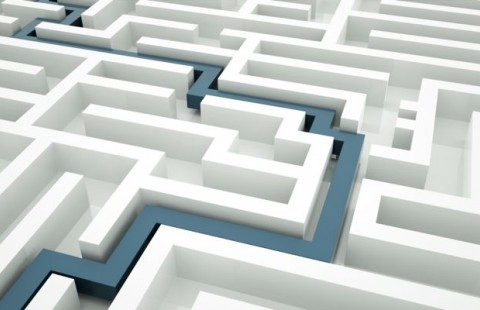
Training - preparation of the SWOT analysis and strategy
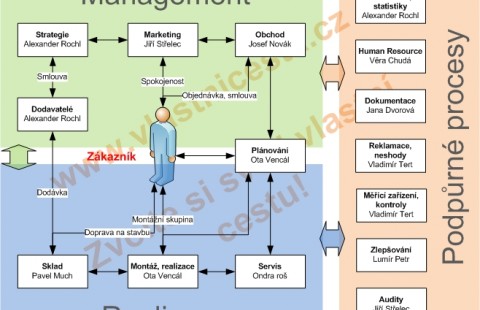
Company Management System of Quality Step by Step - ISO 9001
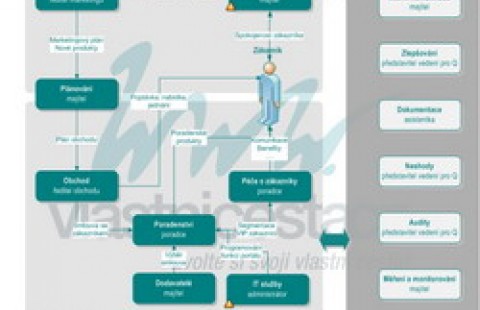
Process map acc ISO 9001 - business offer
3. Subsequently, in the determined failures, a mode how to prevent them will be established, and the entire analysis can be started again – this time in order to assess the efficiency of the measures taken to prevent the failure and detect new risk failures.
FMEA application in successive steps
**The Pre-work**
Prior to introducing the method, you need to take a few steps that will help you carry the FMEA out correctly.
1. First, you have to determine exactly what you want to analyse, for instance, which part of a product, what part of a process. For this purpose, we can utilize, for example, the SIPOC method, the Process Map, or we can establish a particular part for assessment.
2. Then, you set down clearly the requirements for the product to be analysed. Here we can take advantage of the QFD and the C&E Matrix methods.
3. Now it is necessary to call together a team of experts who have to do with the product being analyzed and who will be applying the FMEA. It is crucial that this step is taken with all the care, for if a service worker is left out of the team when designing a new product, for instance, you will miss a valuable source of knowledge about potential problems.
**The Method**
1. Subsequently, a list of all potential problems that might arise is made into a table (here you can take advantage of the Brainstorming method). Ideally, you could utilize a tool, an FMEA form, for instance, where you write down a sigle problem on every line (the so-called Failure Mode).
2. Now, each problem will be assigned its consequence - once again, one problem - one consequence.
3. Then, next to each problem, you put down possible causes of the same - again, one cause - one line (the Ishikawa diagram method can be used here).
4. Afterwards, for each problem, its consequence and cause, you write down the way to detect such a problem or, possibly, to make sure it does not arise.
5. Once you have arranged everything in a table, start assigning coefficients.
- Initially, we begin with the consequences of failures and, based on their severity, assign coefficients from 1 to 10, where 10 is the worst possible. (assignment of the so-called „Severity“ coefficient)
- Subsequently, we take the individual failure causes one by one and, based on their supposed occurence, again assign coefficients from 1 to 10, with 10 being the worst possible. (assignment of the so-called „Occurence“ coefficient)
- Then we check the so-called inspection mechanisms which are supposed to detect or prevent potential problems, and assign them again coefficients from 1 to 10, with 10 being the worst possible conditions. (assignment of the so-called „Detection“ coefficient)
6. Subsequently, by multiplying all the coefficients in a particular line („Severity“x“Occurence“x“Detection“) we get the so-called RPN number which we write down again on that given line. This RPN number indicates the risk rate of the given problem.
7. As soon as we have checked all the lines, it will be time to assess all the RPN numbers and identify those we will pay our attention to (using the Pareto method looks most appropriate here). These numbers will be accompanied by measures we will take to minimize their occurence, plus we add the deadline date and the responsible person.
8. We execute the measures established in the previous point.
9. Now we can proceed to the next step which is to assess the individual problems again, their consequences and find out whether the measures we have taken are appropriate.
Suppose the FMEA is well documented, it can be utilized in designing other similar products or services in the future.
The use of FMEA in examples
The FMEA method is applicable in many types of products, and it is very often even called after those types, so we can find a DFMEA – which is an FMEA applied in a product design (Design FMEA), a PFMEA – which is an FMEA applied in a process (Process FMEA), an S/C FMEA – which is an FMEA applied in a system or a concept (System/Concept FMEA). Naturally, an FMEA can be utilized to assess a project risks, services being provided, a software design.
FMEA can be applied in:
This method is well applicable perhaps in all possible branches of business where we want to improve something, may it be production, development or provision of service.
Description of the method prepared and compiled by "Jaromír Kocurek":jmkocurek@yahoo.com, a consultant
If you need training / lectures on the above method, feel free to contact our "consultants":http://www.ownway.eu/consultants/