With a company´s management growing ever more demanding and with the necessity to employ more and more processes, a need to emulate is also arising. The process map is a simple quality assurance tool designed to illustrate on the top level everything that the company´s management has to control.
The basis of modern management is a visual modeling or using infographics. They make it easy on one page, to understand the issue or the functioning of the company. These include process map.
Plenty of managers either hear or speak about map of processes recently. It is a term widely spread by new version of ISO 9001:2000 standard. The standard puts the accent on a process control and a new term a map of processes has been created.
WHAT IS MAP OF PROCESSES?
A map of processes is visual and transparent chart or, if you like, a model of main processes controlled in a company. It is a part of the highest level of the management system, so called the quality management system. As the highest level part is meant the level of a quality manual in an imaginary pyramid of a quality system. Simply said, everyone looking at this map can see:
- what processes exist in a company
- how processes are organized
- who is responsible for processes
- interaction of processes
- special areas covered by company
The Map of processes is a tool for simplifying of control and decisions making by management through a system and its processes. The company management only presumes that their keeps a tight grip on the company without the map of processes or another illustration. Of course, only if it is not one to ten employees‘ company. Possibility of latent processes formation is much bigger without the map of processes. Unfortunately it happens very often that quality system and hence management (ISO 9001 standard describes a system how to do business well and to control company) is passed on to a quality management representative and her/his team. Management is only interested in the quality activities just before the execution of planned certification authority‘s surveillance audit. Thus it happens very often that all aspects of planned changes are not thought of. Then unneeded problems are solved subsequently.
Inconsiderable part of the map of processes is its graphics design, which should be good-looking and presentable. The way how the map looks like and user friendliness of the map decide about willingness of the management and the employees to use the map.
WHAT THE MAP OF PROCESSES SHOULD TAKE IN TO ACCOUNT?
Although the final version of the map of processes looks very simple, a plenty of negotiation, re-drawing and changes is done during its creation. The main reason is that during the map of processes creation a whole company system is being set up, authorities & responsibilities are specified and so on. Everything has to be duly worked out with consequences. **Other sub processes, connections, relations and management techniques are based on the map of processes.** What is not worked out by management can hardly be changed and finished by employees. Well prepared map of processes should take in account the followings:
- Top Management and its structure – shall be related to the org chart hierarchy
- Special areas executed in line with business plan
- Responsibilities for main processes – to identify specific persons aligned with the map of processes
- Main relations among processes
- Crucial stream of company products realization – a stream showing added value to company income
- Critical points
- Reporting with possibility to measure quality of the company processes.
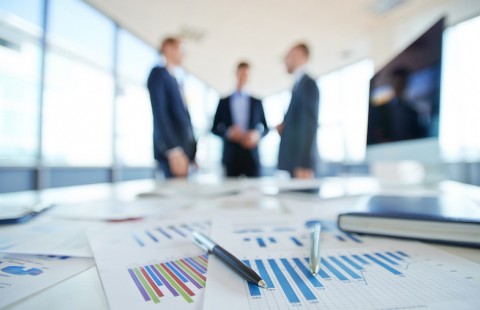
The Real | Interim Manager for Your Changes
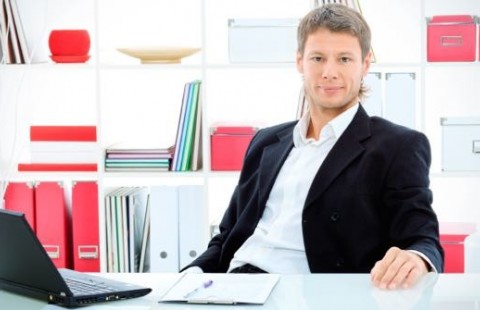
Manager work model
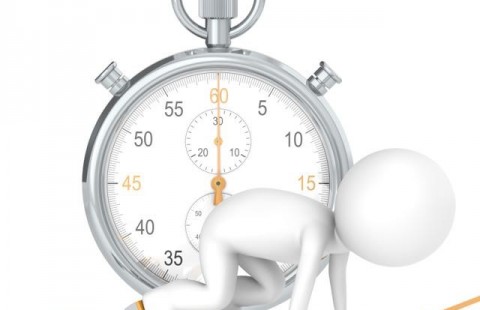
Time management - making use of time effectively
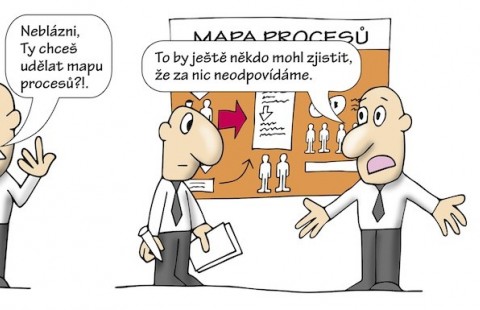
Jak správně tvořit mapu procesů
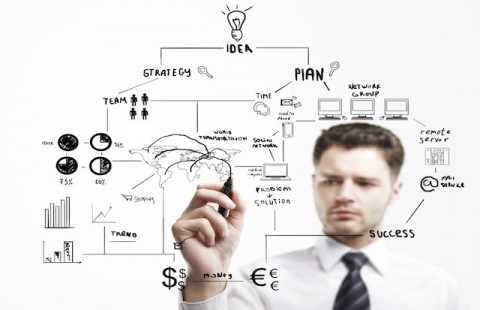
Modelling and setting the processes and procedures - ISO 9001
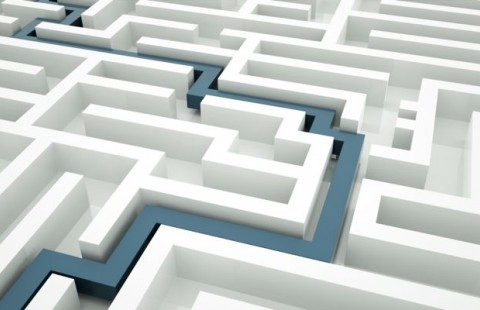
Training - preparation of the SWOT analysis and strategy
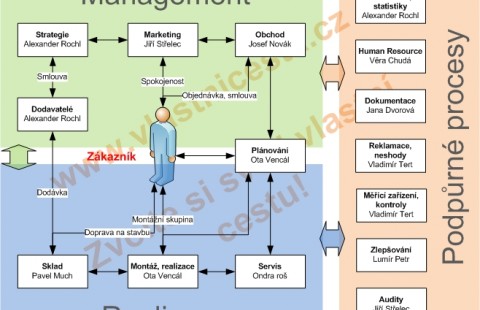
Company Management System of Quality Step by Step - ISO 9001
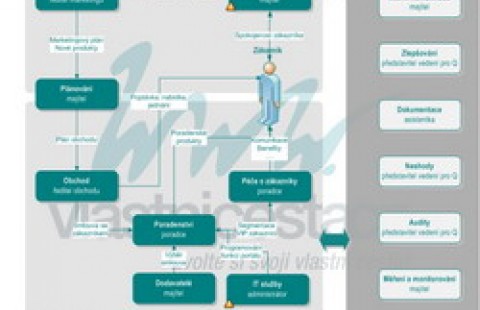
Process map acc ISO 9001 - business offer
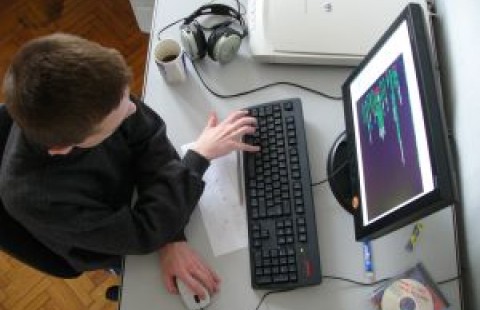
IT staff communication
A design of the map of processes specifies a number of clicks or way length. The way what user (employee) shall to cover until he/she gets information he/she needs. Style of design can streamline employees‘ work or cause loss with continual searching. This aspect is especial important in big companies or global concerns, where the system can cover five or more levels of the system with tens and/or hundreds of processes and sub processes.
The map of processes teaches management to shape their management system, to learn their own processes and finally how to control them effectively!
The basic description of the map of processes meaning has been prepared by consultant who already prepares the maps for years.